We use cookies on our website to give you the most relevant experience by remembering your preferences and repeat visits. By clicking “Accept”, you consent to the use of ALL the cookies.
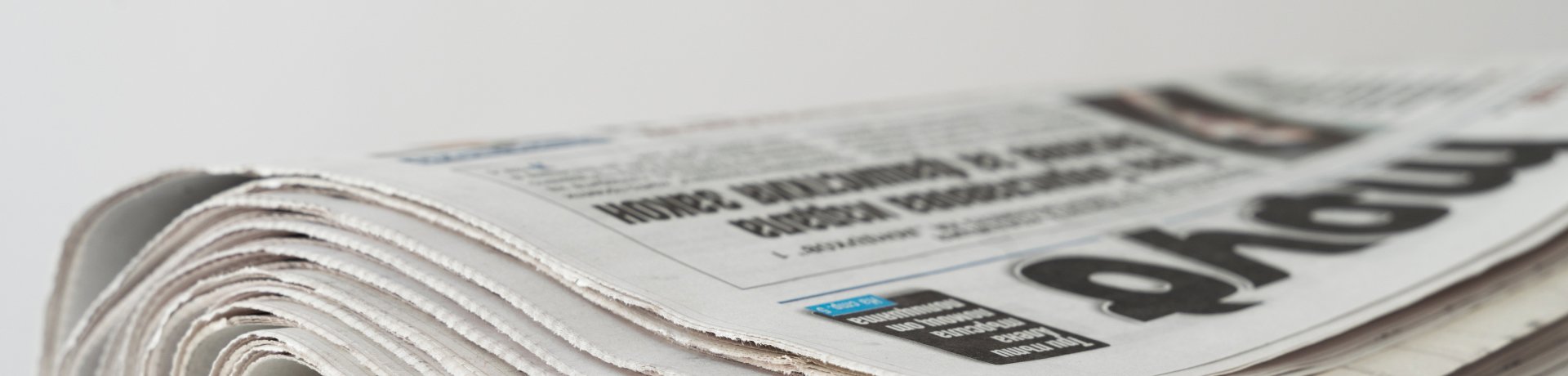
In today's rapidly developing machining field, the guarantee of welding quality is very important.
As a common connection method in machining, the quality of welding is directly related to the performance and service life of products. However, traditional inspection methods often require destructive inspection of welding parts, which is not only time-consuming and laborious, but also may cause irreversible damage to the product.
The emergence of nondestructive testing technology has changed this situation. Through advanced physical testing means, such as ultrasonic testing, X-ray testing, magnetic particle testing, etc., can accurately detect the defects and problems inside the welding parts without destroying the welding structure.
In order to ensure the quality of customers' welding products, Kailai Machinery Factory has purchased ultrasonic non-destructive flaw detector to inspect welding parts. It adopts high-resolution testing equipment and intelligent data analysis system, which can quickly and accurately identify small welding defects, such as pores, slag inclusion, cracks and so on. This not only helps to improve the quality of products, but also can effectively reduce the safety risks caused by welding defects.
Kailai Machinery always adhere to the quality of life, customer-oriented good corporate philosophy, timely personnel training, equipment update, to meet the new needs of the continuous development of the machinery industry, always maintain strong vitality and strong competitiveness of the enterprise, to provide customers with more and better products.